1st October 2021
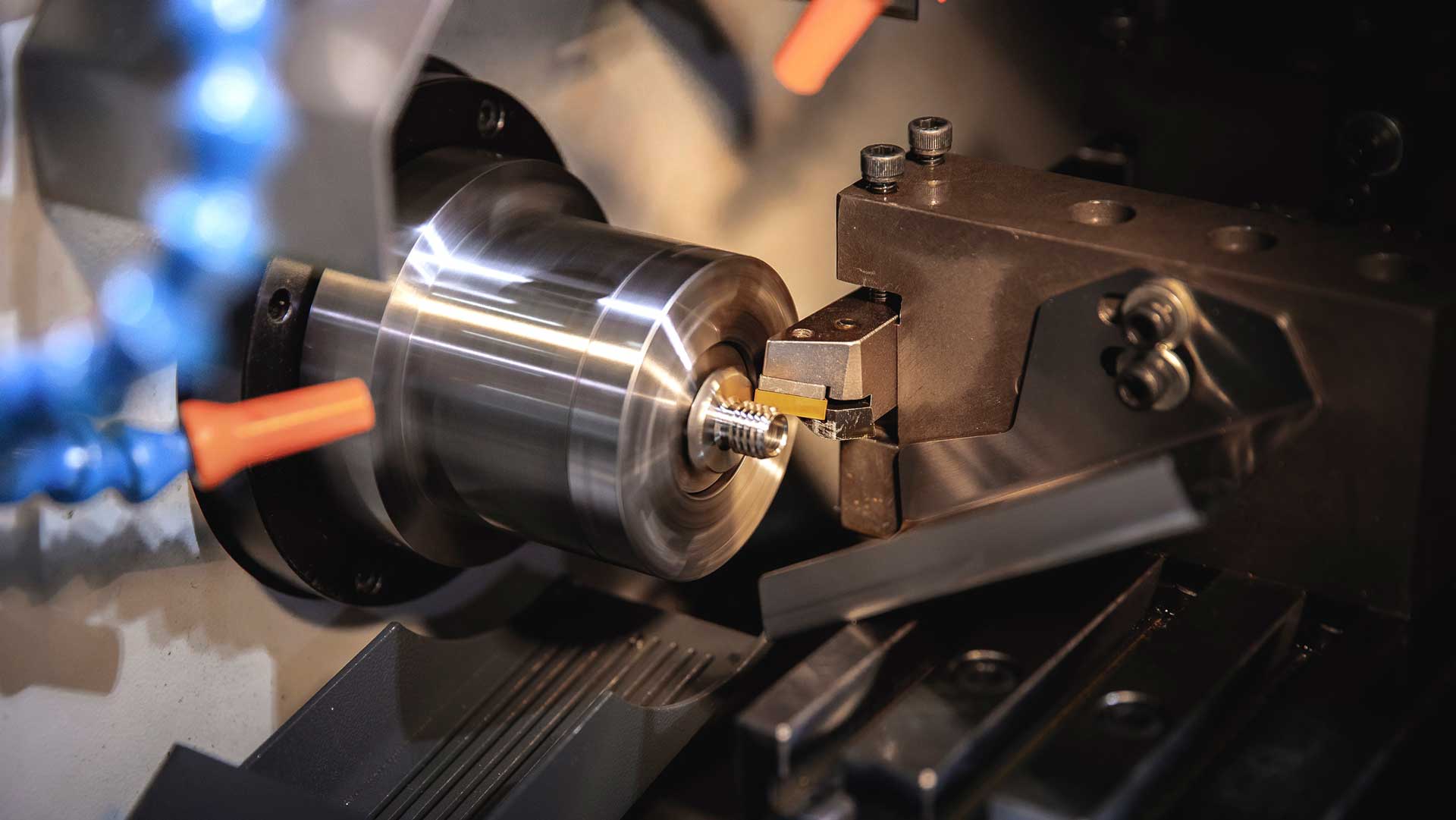
What Is a Screw Cutting Lathe and How Does It Work?
Thread cutting is an essential part of the manufacturing process, but what is a screw cutting lathe and how does it work?
In this article, we describe how screw cutting lathes work and how to select the correct threading insert. At R.D. Barrett, we’ve been supplying engineers and experts with precision tools since 1975, during which time we’ve built up unrivalled industry knowledge and the UK’s largest stock of engineering tools, including screw cutting inserts and machining supplies.
What is a screw cutting lathe?
Screw cutting lathes have been around for hundreds of years, enabling engineers to cut both internal and external threads. Today’s advanced engineering CNC machines provide the same function with a precision that previous generations of engineers could only have dreamed of.
CNC machines use indexable inserts to both cut and form a workpiece. The single cutting point (threading tool) moves up and down the length of a workpiece, removing material to create the thread. CNC machines can cut both internal and external screw threads. To achieve this, the workpiece may need to pass through the CNC several times (known as multiple passes).
The process is known as single point threading. Single point threading enables engineers to cut workpieces at different thread sizes or forms, using a single tool holder. Theoretically, workpieces can be of any size (although they will naturally be constrained by the CNC machine’s size).
But how does a screw cutting lathe work? Let’s take a look.
How does a screw cutting lathe work?
As a workpiece is rotated by the lathe, material is removed from it to form the thread. The movement speed of the cutter, and the rotation speed of the workpiece determine the depth of cut, and how close the threads are (thread pitch). The uniformity of the screw thread is assured by the programmed feed rate per revolution.
CNC machines work at exacting levels, delivering high-quality finished workpieces that require no additional finishing or tooling. Once removed from the CNC machine, they’re ready to use.
The way a cutting tool enters the workpiece can be programmed in a variety of ways, depending on the application. Options include radial infeed, angular in-feeding and modified angular in-feeding. The choice of entry depends on the strength of the material you’re working with.
The quality of thread cutting can be affected by several factors, including tool wear, temperature and a lack of coolant to the workpiece.
Screwcutting in the lathe requires indexable inserts. Indexable inserts come in a variety of sizes, and materials, including high-quality carbide inserts.
We recommend investing in the best quality thread cutting insert to ensure consistent quality and durability. Cheap screw cutting inserts won’t last long and, in some cases, can cause issues including chipping that can damage the workpiece.
For the toughest thread cutting applications, we recommend using a carbide cutting insert. Carbide screw cutting inserts can operate at incredibly high temperatures, accurately machining metals, including steels, carbon, cast iron, and high-temperature alloys.
To select the correct threading insert, you’ll need some information, including:
- Thread form type (THFT)
- Tool type
- Minimum bore diameter (DMIN)
- Grade manufacturers designation (GRDMFG)
- Connection diameter machine side (DCONMS)
The type of thread cutting insert you require will also depend on the material you are working on. Flat geometry inserts are suitable for all types of material while sharp geometry thread inserts are suitable for hard materials including stainless steel. High-quality chip-breaking inserts are suitable for work on hard materials such as stainless steel, where they can be used for longer periods of continuous and unsupervised machining.
At RD Barrett, we’re always on-hand and available to discuss your engineering tool requirements and help you identify the thread cutting inserts you need for the job in hand.
Precision engineering
In the past, thread cutting was performed by experienced machine operators. Today’s CNC machines enable operators to create programmes ensuring repeatability and quality, delivering precision-engineered workpieces and accurate screw threads time after time.
At R.D. Barrett, we’re engineering experts and can provide impartial advice to help you select the correct size inserts for internal threading and external threading. If you require any information or advice on thread cutting or other machine tools, contact us today.