19th October 2020
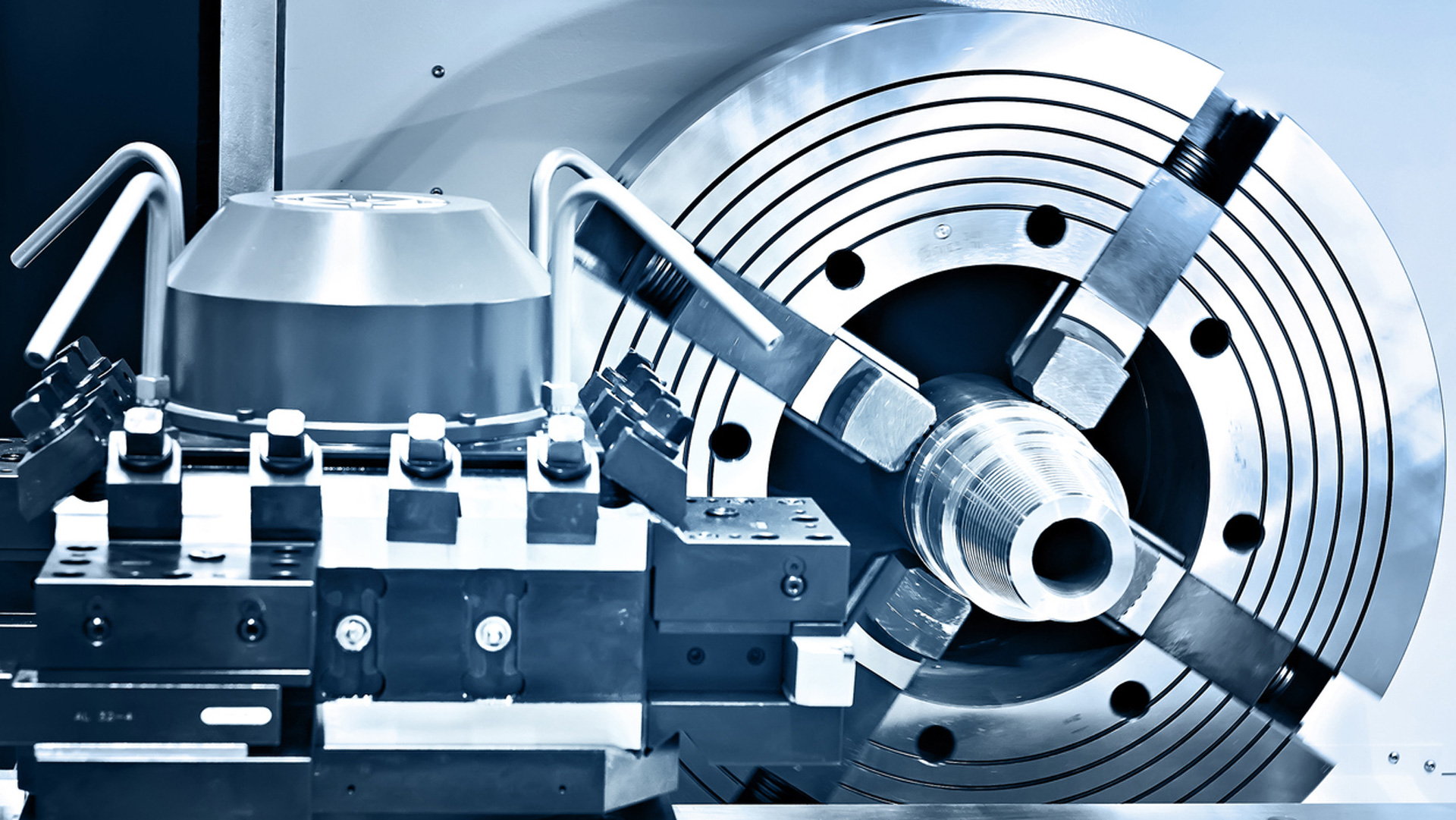
How to Use a 4 Jaw Lathe Chuck
4 jaw lathe chucks are a particular type of chuck designed to safely and securely hold square, hexagonal, wound, and irregular-shaped workpieces. One of the benefits is that 4 jaw lathe chucks are highly accurate, making them preferable to 3 jaw lathe chucks and other options. Centring a workpiece in an independent 4 jaw lathe chuck can be a challenge, but by following our guide, you’ll be able to do it in no time.
What is a 4 jaw lathe chuck?
There are two types of 4 jaw lathe chucks: self-centring lathe chucks and independent lathe chucks.
In self-centring 4 jaw chucks, the jaws move in unison when you turn the knurled ring. Because the jaws move together, the workpiece can be clasped quickly into place. Self-centring chucks are primarily used for square stock, with the interlocking movements of the jaws perfect for rapidly gripping square stock and certain types of round stock.
4 jaw independent chucks have four separate jaws that can be adjusted to grip onto a workpiece. This offers significant advantages. You can use a 4 jaw chuck lathe to safely hold square, hexagonal, wound, and irregular-shaped workpieces, with the independent movement of the jaws enabling accurate adjustment. The pay-off is that they are more time-consuming to set up and configure.
The jaws themselves on both types of 4 jaw chuck lathe can be reversed so that they can hold workpieces by the inside diameter. This offers a much higher range of operation.
Why use a 4 jaw lathe chuck?
4 jaw lathe chucks offer significant advantages over other options such as 3 jaw lathe chucks, including:
- Workpieces can be centred and held with high precision
- 4 jaw lathe chucks can hold square, hexagonal, wound, and irregular-shaped workpieces
- You can turn work off-centre
- 4 jaw lathe chucks can offer better grip on round stock
The disadvantages of using a 4 jaw lathe chuck are the time it takes to set up. However, with our step-by-step guide, it should be fairly straightforward.
Step-by-step guide to using a 4 jaw lathe chuck
Step 1 – Set the jaws to an equal distance
Firstly, start by setting the jaws to an equal distance from the outside edge. This creates space for you to insert the workpiece.
Step 2 – Insert workpiece
Slide the workpiece inside the chuck and gently tighten the jaws against it. Be careful not to overtighten at this stage.
Step 3 – Use a dial indicator
Use a dial indicator and place it on the tip centred on the workpiece stock.
Step 4 – Find the high and low swings
Rotate the chuck until you find the high and low swings. When you’ve found them, move the chuck to the lowest and zero it at this point.
Step 5 – Find the highest swing
Now rotate the chuck and find the highest swing.
Step 6 – Get the calculator out
At this point, you’ll need to divide the highest number by two. Once you’ve calculated this point, rotate the chuck back to this point.
Step 7 – Zero the dial indicator
You’ll now need to zero the dial indicator at this halfway point.
Step 8 – Adjust the axis
At this stage, we can start to adjust the axis. You can move the closest jaw to the dial indicator parallel to the indicator.
Step 9 – Get the dial indicator to zero
Loosen the two jaws and adjust them until the dial indicator reaches zero. Ensure it works on both ends of the rotation.
Step 10 – Repeat the process
You can now repeat the process on the other two axes. Once you’ve got the second axis zeroed, rotate the chuck and ensure that run out is satisfactory. If it isn’t, you’ll need to repeat the process until it is.
At this point, the workpiece should be successfully centred and ready to work on. It should also be simple to remove and replace workpieces of the same size without the need to make any major adjustments. If you’re working on a different stock, simply start the process from step 1 again.
At R.D. Barrett we have a selection of both self-centring and independent 4 jaw lathe chucks in stock and have access to the UK’s largest range of engineering tools. We’re always on hand to discuss your requirements and help you select the right tools for the best job. Give us a call or send us an email today and we can help find the right parts for the best finish.